Add Your Heading Text Here
How to Avoid Packaging Errors and Product Recalls
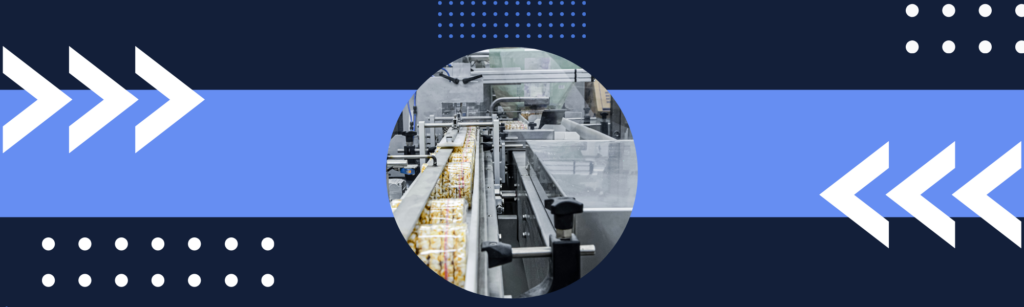
Packaging errors can have serious consequences for food manufacturers, from regulatory non-compliance to costly product recalls and reputational damage.
Incorrect labelling, undeclared allergens, and mispackaged products can pose significant health risks to consumers and lead to financial and operational setbacks for businesses. Preventing such mistakes requires a proactive approach, integrating technology, staff training, and stringent quality control measures.
Common Causes of Packaging Errors
- Human Error: Mistakes in labelling or packaging often occur due to manual handling, miscommunication, or oversight.
- Equipment Malfunction: Faulty printers, scanners, or packaging machinery can lead to incorrect or unreadable labels.
- Supply Chain Issues: Changes in raw materials, packaging components, or formulations that are not properly communicated can also result in mislabelling.
- Regulatory Compliance Failures: Not keeping up to date with evolving food labelling laws can lead to non-compliant packaging.
Ways to Prevent Packaging Errors and Recalls
Implement Robust Verification Systems
Using automated verification systems can significantly reduce human error. Vision inspection technology, barcode scanning, and software-driven label verification help ensure that the correct product and packaging are matched every time.
Conduct Regular Risk Assessments
Assess potential failure points within the packaging and labelling process. Identifying vulnerabilities allows for the implementation of targeted solutions before errors lead to larger issues.
Maintain and Calibrate Equipment
Routine maintenance and calibration of packaging machinery, labelling systems, and printers are essential. Ensuring all equipment is functioning correctly helps prevent printing errors and mislabelled packaging.
Train Employees on Best Practices
Regular training ensures that employees understand the importance of accurate labelling and packaging compliance. Training should cover allergen labelling, batch coding, and quality assurance procedures.
Strengthen Supplier Communication
Transparent communication with suppliers about ingredient or packaging changes is crucial. Implementing clear procedures for updating product information reduces the risk of outdated or incorrect labels.
Stay Compliant with Regulatory Standards
Regulatory compliance is an ongoing responsibility. Keeping up with food safety and labelling regulations ensures that packaging meets all legal requirements and reduces the risk of enforced recalls.
How Hellenic Systems Can Help
Hellenic Systems provides advanced hardware and software solutions that support food manufacturers in ensuring stringent packaging standards that meet to customer specifications. Our technologies help businesses automate quality control, reduce errors, and improve overall efficiency.
- Theia Vision System: An advanced vision inspection system that automatically verifies packaging and labelling accuracy.
- Auto OCM System: A streamlined order control and monitoring system that helps manage packaging workflows efficiently.
- Recipe Management Software: Ensures that ingredient formulations are correctly documented and communicated, reducing the risk of mislabelling.
By implementing these best practices and leveraging advanced technology, manufacturers can significantly reduce the risk of packaging errors, customer fines and product recalls, safeguarding both consumer trust and business integrity.
For more information on how Hellenic Systems can help your business improve packaging accuracy, get in touch for a chat.